Data Loggers: 5 signs of high-end monitoring solutions
You have just shipped kidneys for an organ transplant surgery across the country, only to find out that it was left on the plane and never made it to the surgeon’s table. Though unlikely, over 540 transplants experienced similar delays and “near-misses” due to little-to-no value placed on shipment visibility.
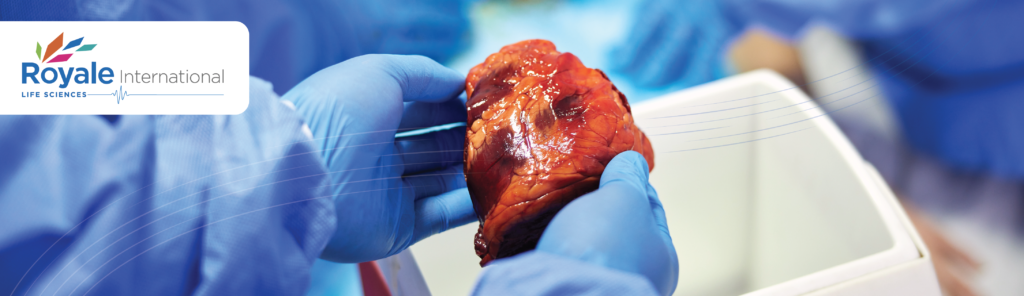
According to Supply Chain Visibility Statistics, supply chain disruptions can cost up to $5.2 million per incident – that’s a total loss of $2.8 billion considering the number of “near-miss” organ transplants mentioned above. Monitoring solutions thus, are vital to mitigate supply chain risk and ensure viable products for patients, researchers and other end-users.
On one hand, monitoring via Data Loggers is not a new concept. On the other hand, the advancement of Internet of Things (IoT) and 5G network capabilities has enhanced various loggers in the market. Royale International’s industry experts have highlighted five key challenges that can be addressed via high-end monitoring solutions:
Learn more about Data Loggers before you continue?
1. “What data is measured?”
There are a handful of factors that can affect a shipment’s integrity or viability throughout transit. Evidently, a high-end data logger should be able to track other metrics to achieve high visibility and support data-driven decision making:
- Light
This helps you understand how often and when the package is opened. In addition, light-degradation can happen to certain drug products, affecting their appearance, potency or adverse immunogenic effects.
- Humidity
There is a risk of contamination when certain Life Sciences products, such as biologics or APIs expose to a humid environment. At the same time, humidity also affects the handler’s susceptibility to viruses, which poses a risk when handling virus samples throughout transit.
- Shock and Motion
Temperature-controlled shipments use specialised packaging – vials, dry shippers, blood bags, and PCM packages. Dropping or hitting the packaging risks leakage of liquid products and reduces viability of temperature-controlled shipments.
2. “How accurate is the data?”
Timely and accurate shipment data enhances decision-making and improves responsiveness. Therefore, it is important to pay attention to the measure frequency of a Data Logger. For example, let’s take a logger calibrated to send temperature data every hour. It would be useless if its latest report shows a temperature excursion that took place 20 minutes ago. There would be no way to reverse a compromised life sciences product.
The reality of real-time tracking is that it is never 100% accurate. However, the best solution is working with loggers that have a 3-Point Calibration for high temperature accuracy.
3. “What about its temperature range?”
Temperature-controlled logistics solutions should offer appropriate temperature ranges for various products. This differs from specialised warehousing for blood samples that would only need data logger checking under a Controlled-Room Temperature (CRT) range. Certain products require cryogenic, dry ice or even refrigerated temperatures.
Consequently, having a one-stop monitoring solution that can handle a wider temperature range can enhance shipment flexibility and reduce cost compared to seeking multiple options that handle shorter ranges.
4. “How often is the data logger handled?”
As a shipment is handled by various personnel in the supply chain, being able to select a logger that only needs to be calibrated during the packing process, and when the shipment is dropped off is ideal. This reduces the risk of comprising the logger and its data. Moreover, it encourages seamless handling throughout the supply chain.
5. “Is it certified?”
Ultimately, the above points would not be relevant if the Data Logger is not certified by governing bodies ensuring its quality. More than a document, this can reflect a logistics provider’s due diligence to educate their supply chain partners, which includes their couriers.
Royale International’s Life Science solutions
At Royale International, our Life Sciences Industry Experts have developed a Quality Management System (QMS) based on WHO guidelines. Consequently, this QMS serves as quality guidelines for our monitoring solutions: our validated equipment includes state-of-the art 5G Data Loggers that enhances visibility for any temperature-controlled shipment.
In addition, our loggers have condition sensors that collect real-time temperature, light, humidity, shock and motion data at 2-minute intervals through 5G connectivity. Location tracking leverages its extensive 400+ global network via cellular, Wi-Fi and GPS tracking. Aligned with our temperature-controlled solutions, our loggers can monitor from cryogenic to CRT temperature ranges.
Our industry experts have procured these high-end Data Loggers that are ISO 17025 certified which provides accessibility to its calibration certificate, and is NIST traceable. Additionally, leveraging our longstanding partnerships, major airlines accept our monitoring solutions.
Want to preview our Data Loggers?
“High-end, high return”
It’s no revelation that temperature-controlled products benefit from high visibility via monitoring solutions in its supply chain. Certainly, understanding what distinguishes a high-end Data Logger against its less advanced models can greatly mitigate shipment incidents and failures. Royale International’s temperature-controlled solutions offer monitoring solutions via our Data Loggers. We commit to a reliable, real-time and accessible shipment tracking through our platform. Contact our experts for your high-end monitoring solution.
Need a high-end monitoring solution? Contact our experts lifesciences@royaleinternational.com
Check out how Royale handled clinical trial shipments here: https://www.royaleinternational.com/2022/12/clinical-trial-shipments/